In the very near future I’ve got 400 blind holes to thread in 100 parts made in 6000 series aluminium. The desired threads are M4-0.7 and M6-1 and the milled holes are just 6.5 mm deep. The threads need to be concentric with the minor diameter and perpendicular to the surface of the stock. And the thread needs to extend to within about one pitch of the bottom of the holes.
With relatively small female threads the best option is a tap. While I can machine these threads on either my manual lathe or CNC mill this is a challenge, primarily due to the relatively small minor diameter and the set-up time for each part.
Cutting this many threads with a tap by hand is going to be time-consuming. The hand process is to mount the tap in a chuck, mount the stock in a machine vice, clean the tap and apply lubricant to the hole and hand-rotate and feed the tap to start the thread square. Now release the tap from the chuck, transfer the stock with seated tap into a bench vice, fit a tap wrench, and gently cut the thread ‘feeling’ for the tap bottoming out. Repeat 400 times. After a few dozen holes this becomes quite tedious and each hole takes about 5 minutes to finish after you get into the swing of the process.
Graded taps (taper, plug and bottoming) for relatively deep through-holes and blind holes reduce the set-up time because the taps become self-centering, at the expense of additional taping operations. The use of graded taps also reduces the cutting torque which is particularly useful in relatively hard materials. But for through–holes in thin material or relatively shallow blind holes alignment by eye can readily lead to threads that are not perpendicular to the stock upper surface. Eye alignment when cutting external threads with a die is even more precarious, often resulting in drunken threads.
But there is a more efficient way of cutting repetitive threads using a drill press or mill using a reversible tap chuck.
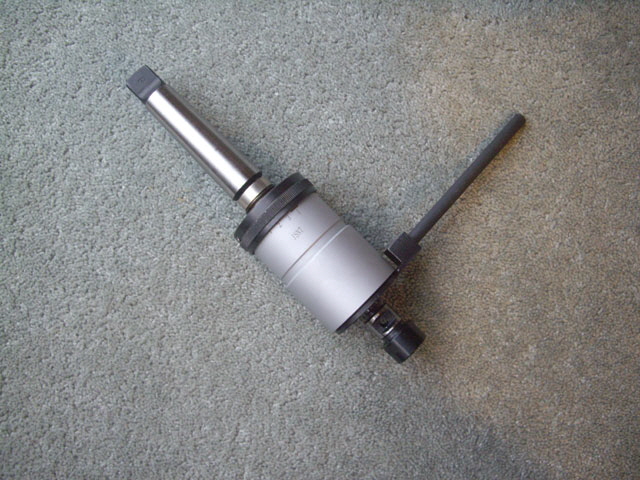
Figure 1. J467 Reversible Tap Chuck
As it happens I have a Model J467 reversible tap chuck that I purchased with my lathe and mill about 20 years ago. I have never had cause to use it until now (in fact the tool was still sealed in its original plastic bags). This particular tap chuck came with two collets suitable for tap shanks from 4 to 7 mm. It didn’t come with any instructions so I need to figure out how it works and how to use it.
The principle of operation is that the chuck feeds the tool with the rotation of the spindle until the tool encounters a resistance greater than the settable conical clutch and the tap stops rotating. The operator (or under CNC control) reverses the feed and the chuck engages a planetary gear set that reverses the tool rotation allowing it to retract gracefully following the cut thread profile. The reverse rotation is a factor of two or more faster than the spindle speed depending on the planetary gear ratio. The chuck also allows for axial movement of the tap (say 12 mm or ½”) between forward and reverse feed engagement which prevents over-feed.
In use the clutch must be set so that it slips well before the tap breaks, and the feed and reverse feed must be appropriate for the thread pitch and spindle speed. While the chuck can operate with a spindle speed of about 1,000 RPM slower is better until you get a feel for the tool. An appropriate cutting fluid is recommended for the stock.
Straight flute taps can be used for through-holes but they tend to push the swarf into the hole ahead of the tool. For machine taping a spiral fluted tap is recommended because the swarf path is toward the shank of the tool.
As it happens I have some spiral fluted M4-0.7 and M6-1 taps purchased specifically for this job but the M6 taps have a significant lead-in taper because the original part design had through-holes. I need a bottoming tap with a lead-in taper of less than 1.5 thread pitches because I need every mm of thread engagement I can get and the holes are relatively shallow. The ISO Standard tap lead-in taper form that I need is E or F but the best that I can find locally is C. Rather than wait for some new taps I simply ground the end off one of my M6 taps and re-ground an approximate 1 mm long taper by hand on a bench grinder. I tested the re-ground tap by hand in 12 drilled blind holes and it cuts 6000 series aluminium like a hot knife through butter with a fully formed thread to within 1 mm of the drill tip point angle at the bottom of the hole.
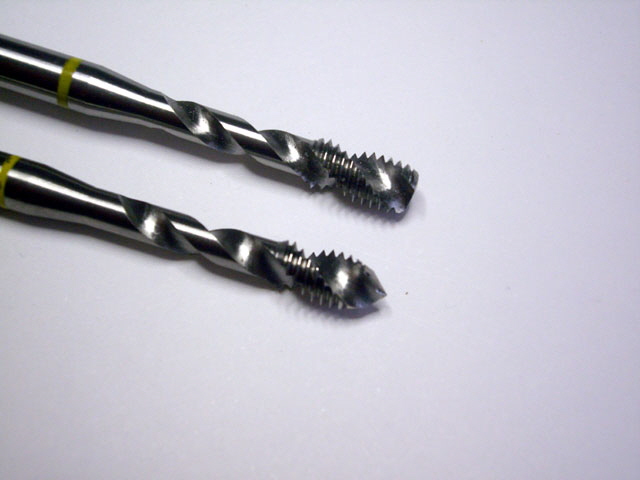
Figure 2. Ground Taper M6-1 Spiral Tap
Time to set up the reversing tap chuck.
The first task is to set up a stop for the torque arm that extends out from the body of the chuck (this isn’t a handle). I suspect that this provides a reference for the planetary gears to stop them rotating with the chuck body. A simple rod or bolt extending vertically from the machine base does the job nicely. I mounted a bolt in the tool post tee nut slot which was conveniently located.
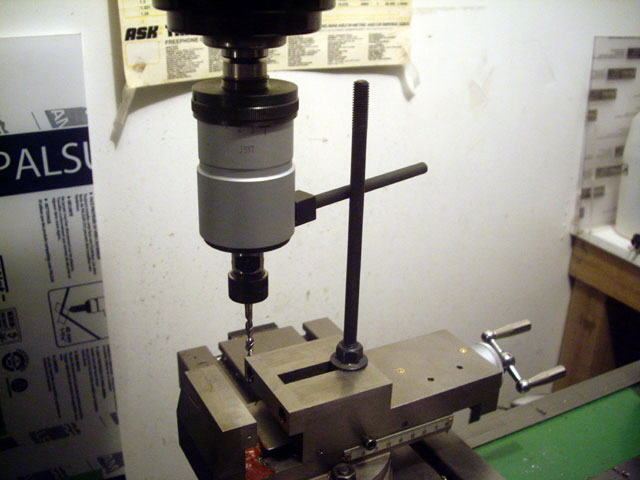
Now fit the appropriate Morse taper and attach the chuck to the drill or mill spindle. It needs to seat clean and tight as it doesn’t have provision for a spindle retaining bolt.
The spindle speed depends on the material and the diameter of the tap. I recommend starting slow (say 120 RPM) until you get the hang of the tool. “Slowly, slowly catchy monkey.”
Next up fit the tap to the chuck. In addition to the collet which centres and retains the tap there are two grub screws that provide the positive drive to the square section shank at the root of the tap. These need to be tightened to contact the sides of the square section to prevent the tap spinning in the collet.
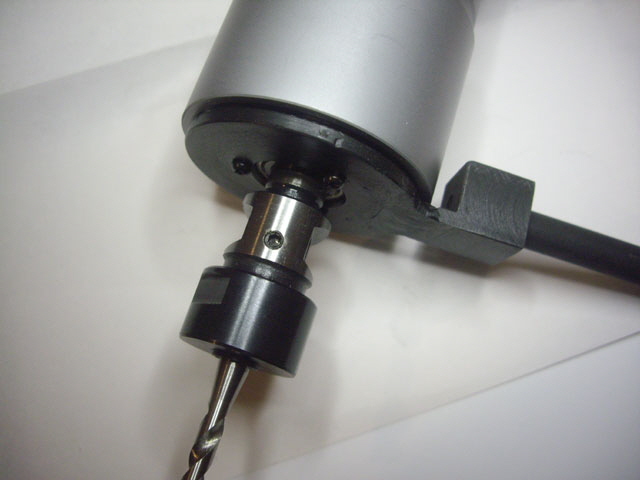
Figure 4. Tap Drive Grub Screw
Now mount the stock with the appropriate diameter hole (complete with lead in chamfer) for the tap in a machine vice or similar. The stock needs vertical support against upward and downward movement, but it can be free to move laterally which helps the tap self-centre and eases initial alignment. For through-holes allow sufficient clearance for the tap to clear the bottom of the hole without hitting anything important. I used the compound slide machine vice with the carriage tee bolts finger-tight to provide some lateral movement. I’ll be using a slotted fixture when I get on to tapping my production parts for rapid direct alignment.
If you are tapping a limited depth thread (not bottoming) then use a spindle stop or note the feed gauge setting for the desired thread depth.
Align the hole with the tap, brush off any swarf from the last operation, and apply an appropriate cutting fluid.
Finally we need to adjust the chuck friction clutch by turning the knurled cap on top of the chuck. Clockwise increases the clutch torque setting. There are graduations on the tap body with index numbers for increasing torque settings. Large taps require more torque. Increase the torque progressively with trial cuts between adjustments until the tap cuts the thread without the clutch slipping. I ended up at just below 4 for an M6-1 tap in 6000 series aluminium.
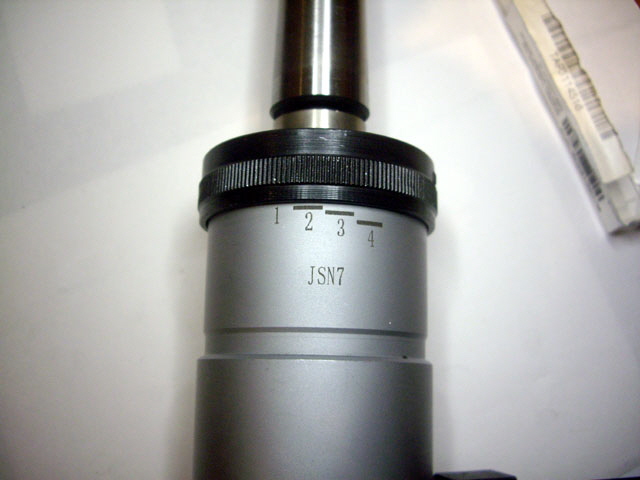
Figure 5. Clutch Setting (Current setting about 1.5.)
Start the spindle forward and gently feed the tap into the hole. When the chuck clutch starts to slip reverse the spindle feed and the tap will reverse and clear the hole. For through-holes or limited depth threads reverse the spindle feed (upward) once the desired depth of thread has been achieved.
Once the reversing chuck is set up threading subsequent holes takes just a few seconds. Align the new hole, apply lubricant, start the spindle forward, feed the tap, reverse the spindle feed and guide the tap clear of the threaded hole.
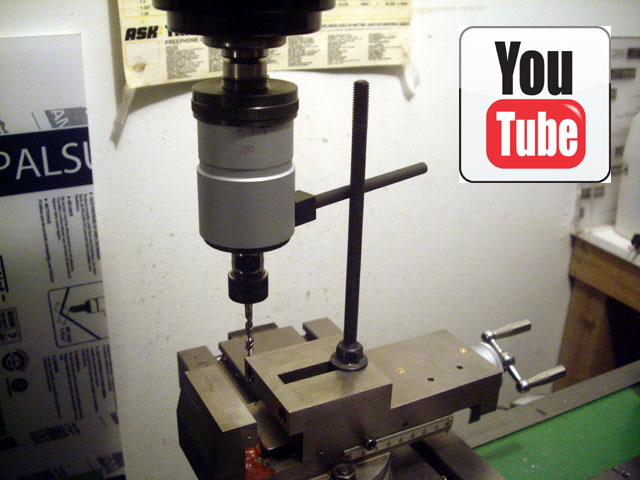
Figure 6. YouTube Video of Reversing Tap Chuck in Operation (Click on image to link to the video.)
You’ll see on the video that on subsequent tapping operations the reversable tap chuck collet will jump upward about 12 mm at the start of engagement with the stock. This is simply the collet re-seating from reverse to forward drive from the previous operation and is not detrimental to the thread form.
|